Installation Guidelines for Aluminum Busbars
When diving into the world of aluminum busbars installation, one must wield a meticulous hand — first and foremost, ensure that the mounting surface is not just clean but also dry. Why? Because neglecting this crucial step can pave the way for corrosion to sneak in like an unwelcome guest at a party, jeopardizing that all-important secure fit.
Now let’s talk alignment — oh, it’s absolutely paramount! Those busbars need to be positioned with precision before you even think about tightening those fasteners. Imagine trying to thread a needle while riding a rollercoaster; that's how critical proper placement is! And don’t forget your insulated tools during this electrifying endeavor; they’re your safety net against unforeseen electrical shocks lurking around every corner.
Oh, and let’s not gloss over torque specifications when securing those connections! It’s a delicate dance: too much torque could spell disaster for your busbars, while too little may leave you with loose connections that threaten to derail performance entirely. And spacing—ah yes—the unsung hero of safe operation! Ample room between busbars isn’t merely suggested; it’s essential for accommodating thermal expansion like a cozy blanket on a cold night.
Adhering to these guidelines will weave together safety and efficiency in the intricate tapestry of your electrical system.
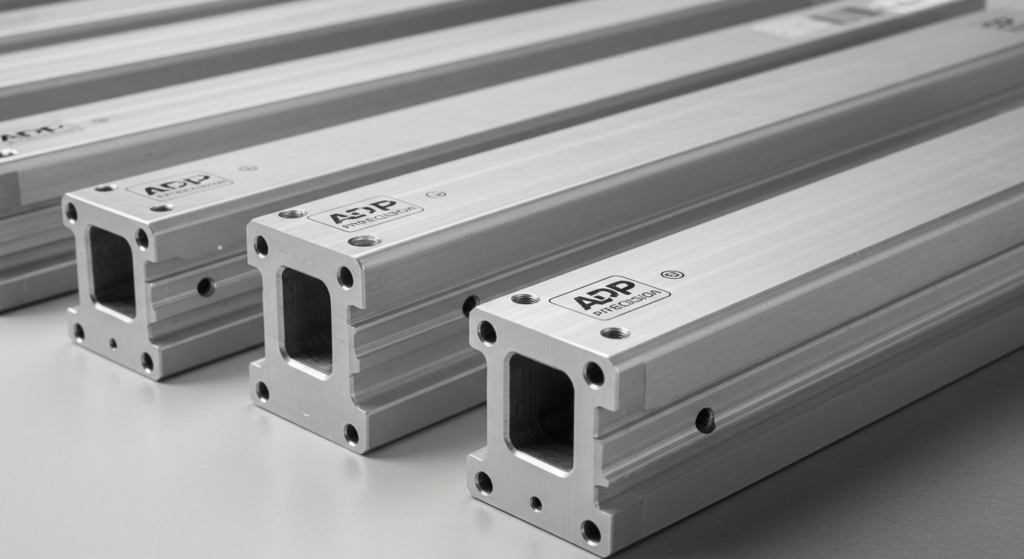
Best Practices for Safe Installation
Ensuring the safety of aluminum busbar installations is no simple feat; it begins with meticulous planning, a labyrinthine process that demands attention to every detail. First and foremost, one must scrutinize the installation site for lurking hazards—overhead obstacles that threaten to interfere, or woefully inadequate ventilation that could spell disaster in an instant. The importance of proper training cannot be overstated; all personnel involved must dive deep into understanding not just the tools and equipment at their disposal but also the intricate specifications tied to aluminum busbars themselves—like those elusive torque settings critical for secure connections.
As installation commences, keeping a workspace spick-and-span becomes paramount—a chaotic environment only invites accidents through its open door. Equip yourself with personal protective gear fit for battle against electrical shocks and other lurking dangers! And let’s not forget: securing each component robustly is non-negotiable; even a momentary lapse can lead to catastrophic disconnections. Regular communication among team members transforms into a lifeline—it ensures everyone remains acutely aware of their roles and potential perils, creating an atmosphere where safety reigns supreme throughout this complex endeavor.
Maintenance Tips for Longevity
Maintaining aluminum busbars is not just important; it’s absolutely vital for their durability and peak performance! Picture this: regular inspections zeroing in on those crucial connections—it's like a health check-up for your electrical system, searching for any sneaky signs of corrosion or wear that might be lurking about. And let’s talk cleanliness—it’s the unsung hero of conductivity! A mere accumulation of dirt and debris can spiral into overheating disasters and efficiency drops. So, keeping every surface spotless? Non-negotiable!
But wait, there’s more! Alongside routine cleaning, don’t forget to periodically tighten those connections. Loose joints are troublemakers—they crank up resistance and generate heat like nobody's business. Keeping a meticulous record of maintenance schedules is also essential; it allows you to track the condition and performance of your busbars through time's relentless march. By sticking to a proactive maintenance plan, operators can stretch the lifespan of these aluminum wonders, ensuring reliable energy distribution flows smoothly without a hitch!
Regular Checks and Care
Periodic inspections of aluminum busbars are absolutely paramount for guaranteeing peak performance and safety—there's no skirting around that fact. Technicians need to engage in meticulous visual examinations, hunting for any telltale signs of corrosion, wear, or physical damage lurking in the shadows. Measurements taken at electrical connections can reveal troubling irregularities that might compromise efficiency; it’s all about keeping an eye on those details! Ensuring that connections remain snug and free from oxidation is not just a good practice—it’s essential for preserving conductivity.
And let’s not overlook the critical importance of cleaning these busbars every now and then! The accumulation of dust and debris isn’t merely an aesthetic issue; it can trigger overheating and lead to catastrophic electrical failures. A gentle touch with a soft cloth or brush to whisk away contaminants will go a long way in safeguarding the integrity of those busbars. By scheduling regular maintenance, you’re not just playing defense against unexpected failures—you’re actively extending the lifespan of your entire system.
- Regularly check for signs of corrosion or wear on busbars.
- Measure electrical connections to ensure proper efficiency.
- Verify that all connections are tight and free from oxidation.
- Clean busbars periodically to prevent dust and debris buildup.
- Schedule routine maintenance to identify issues before they escalate.
- Document all inspections and maintenance activities for future reference.
- Educate technicians on best practices for busbar care and maintenance.
Custom Solutions Offered by AP Precision
AP Precision grasps the reality that every project unfolds with its own distinctive set of demands, which is precisely why they provide bespoke solutions for aluminum busbars. Their team dives deep into collaboration with clients, meticulously uncovering specific requirements to ensure designs resonate harmoniously with the intended application. With a wealth of customization options—ranging from size and configuration to conductivity—clients are empowered to unlock peak performance for their electrical systems.
Moreover, the manufacturing process is infused with cutting-edge technologies, paving the way for engineering excellence and high production standards. This unwavering dedication to quality guarantees that each custom busbar not only meets rigorous safety criteria but also excels in performance benchmarks. Clients can anticipate not just functionality; they will receive durability as well—a hallmark that solidifies these tailored solutions as an exceptionally reliable choice across diverse industrial landscapes.
Tailoring Busbars to Client Specifications
AP Precision revels in the art of crafting bespoke aluminum busbars, meticulously tailored to cater to the distinct demands of an array of industries. Recognizing that one size simply doesn't fit all, this innovative company engages in a dynamic dialogue with its clients, delving deep into their unique specifications. This intricate process entails a thorough assessment of operational environments, load requirements, and those pesky installation hurdles that can trip up even the best-laid plans—all aimed at forging busbars that not only optimize efficiency but also bolster reliability.
But wait—there’s more! The magic doesn’t just stop at dimensions and capacities; oh no! AP Precision's prowess extends into specialized coatings and finishes designed to fend off corrosion or elevate aesthetics based on what tickles their clients’ fancy. With cutting-edge manufacturing techniques and premium materials at their fingertips, each crafted busbar is engineered to not just meet but frequently surpass industry benchmarks. This unwavering commitment to customization is pivotal in delivering products that resonate perfectly with performance expectations across a kaleidoscope of sectors.
Environmental Aspects of Aluminum Busbars
Aluminum busbars present an intriguing tapestry of environmental benefits, woven together by the material's feather-light quality and remarkable conductivity. This efficiency—oh, how it dances through power lines!—significantly curtails energy loss during transmission. But wait! There’s more: aluminum boasts a high recyclability factor that positions it as a champion of sustainable electrical infrastructure. The recycling process is astonishingly efficient too; it demands just a mere whisper of the energy needed to forge primary aluminum from scratch, which in turn slashes carbon footprints with finesse.
In myriad industries, the adoption of aluminum echoes eco-friendly practices loud and clear. By choosing aluminum busbars, companies find themselves harmonizing with the crescendo of sustainability goals while reaping rewards from this material's robust durability and strength. And let's not forget about those recycling programs sprouting up everywhere—they transform the lifecycle of aluminum into something truly spectacular. It significantly cuts down on waste and sings sweetly to the ideals of a circular economy that champions reuse over relentless new production!
Sustainability and Recycling Benefits
Aluminum busbars are increasingly capturing attention for their eco-friendly credentials. The process of producing aluminum emits far fewer pollutants compared to its metallic counterparts, positioning it as a greener option for power distribution systems. Plus, the featherweight characteristics of aluminum make transportation and installation a breeze—further slashing the carbon footprint tied to electrical setups.
But wait, there's more! Recycling is pivotal in amplifying the environmental perks of aluminum busbars. Once they’ve reached the end of their functional life, these materials can be recycled endlessly without sacrificing quality—a fantastic feature that allows them to be reborn in new applications. This circular dance not only conserves precious natural resources but also minimizes waste, harmonizing perfectly with global sustainability initiatives. The simplicity of recycling enables companies to achieve their sustainability targets while championing a thriving circular economy.
Innovations in Aluminum Busbar Technology
The realm of aluminum busbar technology is undergoing a whirlwind of transformation, propelled by the relentless march of materials science and engineering breakthroughs. Picture this: cutting-edge manufacturing techniques like cold forming and die-casting are emerging, enabling designs that dance with precision while boasting enhanced conductivity. These revolutionary methods empower manufacturers to craft busbars that don’t just shed weight but also crank up efficiency, slashing energy losses and turbocharging overall system performance.
But wait—there’s more! The rise of smart technology integration is sweeping across the industry like wildfire. Imagine sensors and monitoring systems seamlessly embedded within busbars, delivering real-time insights into electrical flow, temperature fluctuations, and lurking faults. This newfound connectivity goes beyond mere convenience; it paves the way for proactive maintenance strategies and fuels the evolution of smart grids. With such advancements in load distribution and energy management at our fingertips, it’s clear that integrating these intelligent technologies is fundamentally redefining how electrical systems operate in today’s high-tech landscape.
Recent Developments and Trends
Revolutionary methods in the crafting of aluminum busbars have sparked a seismic shift in their efficiency and versatility across a multitude of industries. Cutting-edge advancements in extrusion techniques and alloy formulations have birthed designs that are not only lighter but astonishingly robust, cranking up conductivity while slashing material costs to boot. These breakthroughs seamlessly cater to the escalating thirst for energy efficiency while deftly navigating the labyrinth of ever-evolving regulatory standards governing electrical applications. Additionally, innovative surface treatments and coatings have made their grand entrance, boasting enhanced corrosion resistance and an impressive lifespan even when faced with the harshest environments.
But wait—there’s more! The emergence of cutting-edge technologies is opening doors to smart busbar systems packed with monitoring prowess. Imagine these systems harnessing IoT (Internet of Things) connectivity to churn out real-time data on temperature fluctuations, load dynamics, and overall performance metrics. This treasure trove of information paves the way for proactive maintenance strategies and meticulously optimized power distribution. And as industries ramp up their commitment to sustainability like never before, there’s a palpable surge towards weaving eco-friendly practices into both the production processes and recycling efforts surrounding aluminum busbars—aligning these innovations beautifully with global environmental aspirations!
Conclusion
Aluminum busbars—oh, what a marvel they are! They deliver a dynamic and efficient answer to the needs of contemporary electrical systems. Light as a feather yet tough as nails, these sleek conduits find their place in an array of settings—from towering commercial edifices to bustling industrial hubs. And let’s not forget: as businesses increasingly champion sustainability, the eco-friendly perks of aluminum—like its remarkable recyclability—only amplify its allure.
Enter AP Precision, a true standout amidst the crowd! This company specializes in crafting bespoke solutions that cater meticulously to each client’s distinct requirements. By marrying cutting-edge technology with an unwavering commitment to safety and durability, AP Precision guarantees that their aluminum busbars don’t just perform—they excel while adapting seamlessly to the ever-evolving landscape of industry standards. What a win-win!