Overview of Busbars
Busbars play a crucial role in electrical systems by providing a reliable means of distributing power. These conductive components are often made from materials like aluminum or copper, with custom aluminum busbars gaining popularity for their lightweight and corrosion-resistant properties. Aluminum alloys are frequently used in manufacturing these bus bars due to their excellent conductivity and mechanical strength. The versatility of custom aluminum busbars allows for tailored solutions that meet specific electrical requirements, making them a preferred choice for various applications across industries. Resources such as aluminum.org highlight the ongoing advancements in busbar technology, emphasizing the significance of high-quality materials in ensuring optimal performance and durability.
Definition and Functionality of Busbars
Busbars serve as essential components in electrical systems, offering an efficient way to distribute electrical power. These conductive strips or bars are often made from materials such as aluminum alloys and stainless steel, which provide excellent conductivity and resistance to corrosion. Custom aluminum busbars are particularly popular due to their lightweight nature and ability to be tailored for specific applications, including busways in rail transportation. The versatility of busbars allows them to be integrated seamlessly within various infrastructures, from commercial buildings to industrial plants.
The functionality of busbars extends beyond mere power distribution. They enable the organization of electrical circuits, enhancing the safety and reliability of electrical setups. Custom aluminum busbars can be designed to meet specific load requirements, ensuring optimal performance while minimizing energy loss. Compared to traditional steel options, aluminum busbars are lighter, reducing installation stress on structures and facilitating easier maintenance. Their application across different sectors, including manufacturing and rail transportation, highlights their importance in modern electrical engineering.
Types of Busbars in Electrical Systems
Busbars are essential components in electrical systems, providing a reliable means of conducting electricity within various applications. Custom aluminum busbars are often chosen for their lightweight properties and high conductivity. They are increasingly utilized in hybrid vehicles, where weight efficiency is crucial. The chassis of these vehicles benefits from improved electrical distribution, allowing for better performance and energy efficiency. Expanded metal designs also enhance the thermal management of busbars, contributing to overall safety and reliability in transportation systems.
Another key type of busbar is made from alloy steels and mild steel, which offer durability and strength in high-load applications. These steel busbars are typically found in industrial environments where the demands for current-carrying capacity and structural integrity are high. As the transportation industry evolves, integrating custom aluminum busbars into vehicle design focuses on optimizing performance while reducing weight. This shift not only improves efficiency but also helps meet environmental standards in modern transportation.
- Improved electrical distribution leads to enhanced vehicle performance.
- Lightweight aluminum busbars are ideal for hybrid and electric vehicles.
- Alloy steel busbars are preferred for their strength in industrial settings.
- Thermal management in busbars is crucial for safety and reliability.
- Custom designs allow for tailored solutions to specific electrical needs.
- Integration of advanced materials supports compliance with environmental standards.
- The evolution of busbar technology aligns with trends toward energy efficiency in transportation.
Custom Aluminum Busbars
Custom aluminum busbars offer a versatile solution across various industries, including automotive, aerospace, and electrical panelboards. These busbars are crafted from high-quality aluminum alloys, which ensure lightweight yet strong components that can withstand demanding environments. The manufacturing process often involves precision milling and advanced machining techniques to achieve exact specifications tailored to specific applications. Utilizing custom aluminum busbars enhances efficiency and performance due to their excellent conductivity and resistance to corrosion, making them a preferred choice for modern electrical systems.
Benefits of Choosing Aluminum Busbars
Aluminum busbars offer exceptional weight savings compared to traditional copper alternatives. This lightweight characteristic simplifies installation processes and reduces the overall structural demands of electrical systems. The manufacturing of custom aluminum busbars often incorporates laminated designs that enhance durability and efficiency. These features make aluminum busbars a popular choice for many engineers seeking reliability in their electrical applications.
Cost-effectiveness is another significant advantage of aluminum busbars. They generally have lower raw material costs compared to copper, making custom aluminum busbars an economical solution for various projects. The packaging of aluminum custom bus products also tends to be more efficient, as they are easier to handle and transport due to their lighter weight. These factors contribute to the increasing preference for aluminum bus bars in modern electrical systems and infrastructures.
Applications of Custom Aluminum Busbars
Custom aluminum busbars are extensively used in various industrial applications due to their excellent electrical conductivity and lightweight properties. Industries such as renewable energy, automotive, and telecommunications rely on aluminum bus bars for efficient power distribution. The solid busbar design of these components allows for optimal performance under high load conditions. Customization, such as manufacturing aluminum bus pipes and laminated busbars, caters to specific requirements in diverse environments, ensuring reliability and longevity.
The versatility of custom aluminum busbars makes them suitable for both large-scale installations and compact systems. Top aluminum bus solutions can be found in substations, data centers, and manufacturing plants where maximizing space while maintaining high conductivity is essential. Stock busbars are often chosen for standard applications, but custom aluminum busbars provide tailored solutions that enhance efficiency and performance in specialized projects.
Industry | Application | Busbar Type | Benefits |
---|---|---|---|
Renewable Energy | Solar Power Systems | Custom Aluminum Busbars | High conductivity, lightweight, durable |
Automotive | Electric Vehicle Charging Stations | Laminated Busbars | Space-saving, increased efficiency |
Telecommunications | Data Centers | Aluminum Bus Pipes | Reliable power distribution, thermal management |
Manufacturing | Production Facilities | Solid Busbars | High load capacity, customized configurations |
Aluminum Busbar Manufacturing
The manufacturing of custom aluminum busbars involves advanced busbar fabrication techniques tailored to meet specific electrical requirements. From the production department, both flexible busbars and rigid busbars are crafted to ensure optimal conductivity and adaptability in various applications. Clients often seek customized busbar solutions to fit the unique demands of their next busbar project, making functionality and efficiency crucial. The process emphasizes precision in the creation of custom bus bars, ensuring they meet stringent quality standards while also providing flexibility for future modifications. Emphasizing innovation in busbar production, manufacturers are constantly improving their methods to enhance the performance of custom aluminum busbars.
Custom Busbar Fabrication Techniques
Fabricating custom aluminum busbars involves precise engineering to meet specific requirements. Different busbar sizes and configurations can be tailored for optimal performance in various applications. Skilled manufacturers focus on the properties of bus bar material, ensuring that the aluminum bar meets standards for conductivity and durability. Techniques such as extrusion and machining are routinely used to create custom bus bars that support effective electrical distribution while accommodating unique design needs.
During fabrication, special attention is given to bus bar joints to enhance reliability and minimize resistance. Value-added busbar services may include surface treatments and assembly options to provide a comprehensive solution for customers. These custom aluminum busbars can be designed to fit seamlessly into existing systems, allowing for efficient integration. Manufacturers often emphasize the importance of rigorous testing to ensure that each product upholds the desired level of performance and durability.
- Customization allows for tailored dimensions and configurations specific to project needs.
- Precision machining ensures a tight fit and minimized electrical resistance.
- Surface treatments can enhance the corrosion resistance and appearance of busbars.
- Quality control measures are implemented throughout the fabrication process.
- Advanced testing methods verify electrical performance and longevity.
- Integration with existing systems is streamlined to facilitate installation.
- Continuous communication with clients helps refine designs and specifications.
Quality Standards for Aluminum Busbar Production
Maintaining high-quality standards in the production of custom aluminum busbars is essential for ensuring reliability and performance. The choice between aluminum and copper bus bars often hinges on their respective functionalities and applications. Aluminum offers significant advantages such as lighter weight and resistance to corrosion, making it ideal for strategic bus bar installations. Thicker bus bars can also enhance the electrical conductivity needed in high-demand situations, ensuring that these bus bar products meet industry requirements.
Adhering to rigorous quality control measures is critical in the manufacturing process for aluminum products. RHI busbar systems, for example, must pass various tests to guarantee their capability in demanding environments. Quality standards encompass not only the structural integrity of custom aluminum busbars but also their performance under different operational conditions. Manufacturers must ensure that their thicker bus bars are tested for durability, electrical performance, and overall efficiency to satisfy both industry regulations and client expectations.
Comparing Aluminum and Copper Busbars
Aluminum busbars offer distinct advantages over their copper counterparts, particularly in terms of weight and cost-effectiveness. Custom aluminum busbars are significantly lighter, making them easier to handle and install, especially in complex bus packaging scenarios. Low voltage busbars benefit from the excellent conductivity of aluminum material, which provides reliable performance in various electrical applications. Quality aluminum not only reduces manufacturing costs but also ensures robust durability, essential for connections involving aluminum connectors. The potential for bus bar fabrication with aluminum reduces strain on resources while delivering effective electrical bus bars suitable for both standard and specialized applications. Ultimately, the choice between aluminum and copper hinges on specific project needs, including performance, cost analysis, and installation logistics.
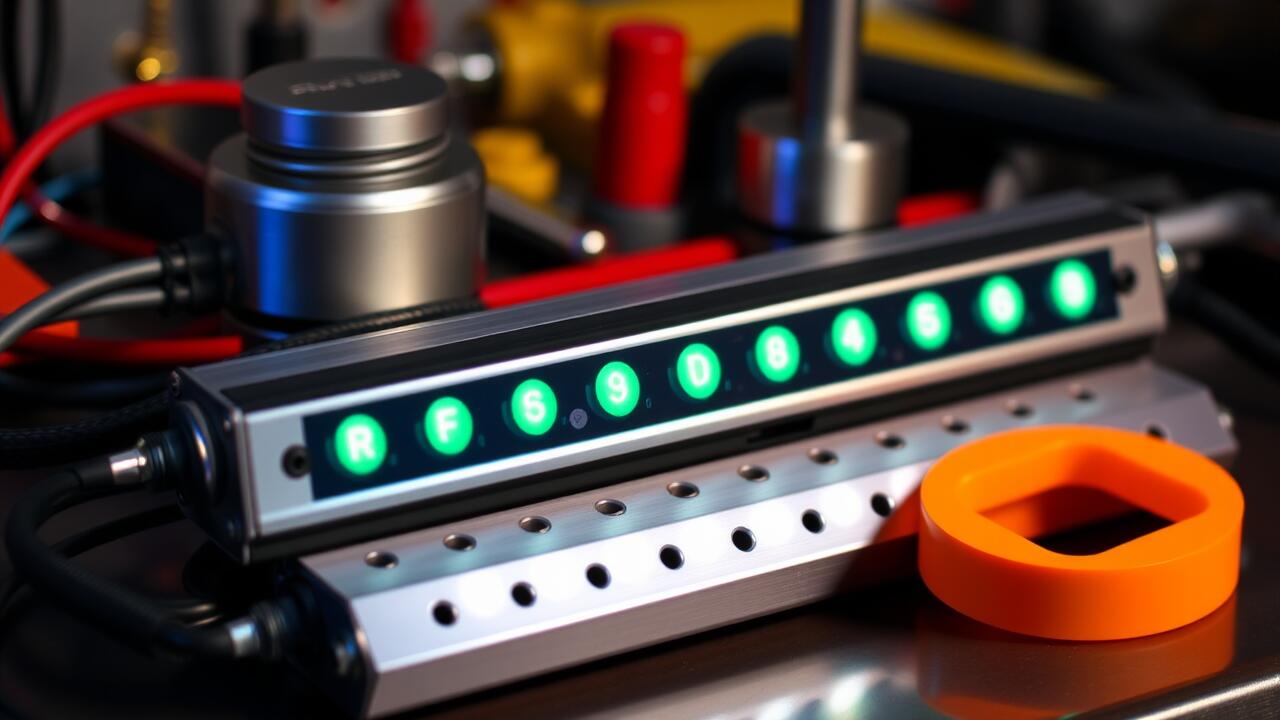
Advantages of Aluminum Busbars over Copper
Custom aluminum busbars offer several advantages compared to copper. They are lighter, making them easier to handle and install, which saves time and labor costs. High-quality aluminum materials also provide excellent conductivity while being corrosion-resistant. This durability ensures that the busses maintain their performance over time, especially in environments exposed to elements like aluminum air. The use of high strength aluminum in these busbars allows for the fabrication of thinner, more compact designs without sacrificing performance.
Cost-effectiveness stands out as a key benefit of aluminum busbars. The lower price of aluminum materials compared to copper translates to reduced overall project budgets. Custom aluminum busbars can be designed with specific dimensions to fit unique applications, optimizing space and enhancing functionality. With robust bus bar connectors, these aluminum pipe systems efficiently deliver power while minimizing energy loss. As a result, choosing aluminum for busbars is often the best option for both economic and practical considerations.
Cost Analysis of Aluminum vs. Copper Busbars
The cost analysis between custom aluminum busbars and copper busbars reveals significant financial advantages for aluminum options. Custom aluminum busbars tend to be more affordable due to lower material costs. American-based aluminum suppliers offer a variety of products, including aluminum angles and standard aluminum extrusions, which facilitate efficient assembly in various bus systems. The use of bus bar fasteners helps reduce installation times and overall project expenses, making aluminum a smart option for budget-conscious projects.
Aluminum's lightweight nature contributes to savings in transportation and handling costs. Aluminum conducts electricity effectively and is often sufficient for most applications, reducing the need for expensive copper solutions. The availability of aluminum rods and just-in-time aluminum metal delivery further streamlines production and lowers costs. These factors highlight why custom aluminum busbars are increasingly preferred in the market, particularly for those looking to optimize both performance and expenditure in their electrical systems.
Busbar Products and Solutions
Custom aluminum busbars serve as vital components in electrical systems, offering a range of solutions tailored to various applications. These busbars can be fabricated from aluminum sheets and coils, ensuring they meet specific requirements for conductivity and weight. The use of seamless bus pipe contributes to a more efficient flow of electricity. Alongside aluminum plates and aluminum round rods, these customizable options enhance transportation product manufacturing. The integration of aircraft alloy steels further strengthens the structural integrity of the busbars, particularly in demanding environments. Electrical busway systems benefit significantly from the versatility of custom aluminum busbars, which can be designed to fit unique specifications and performance criteria.
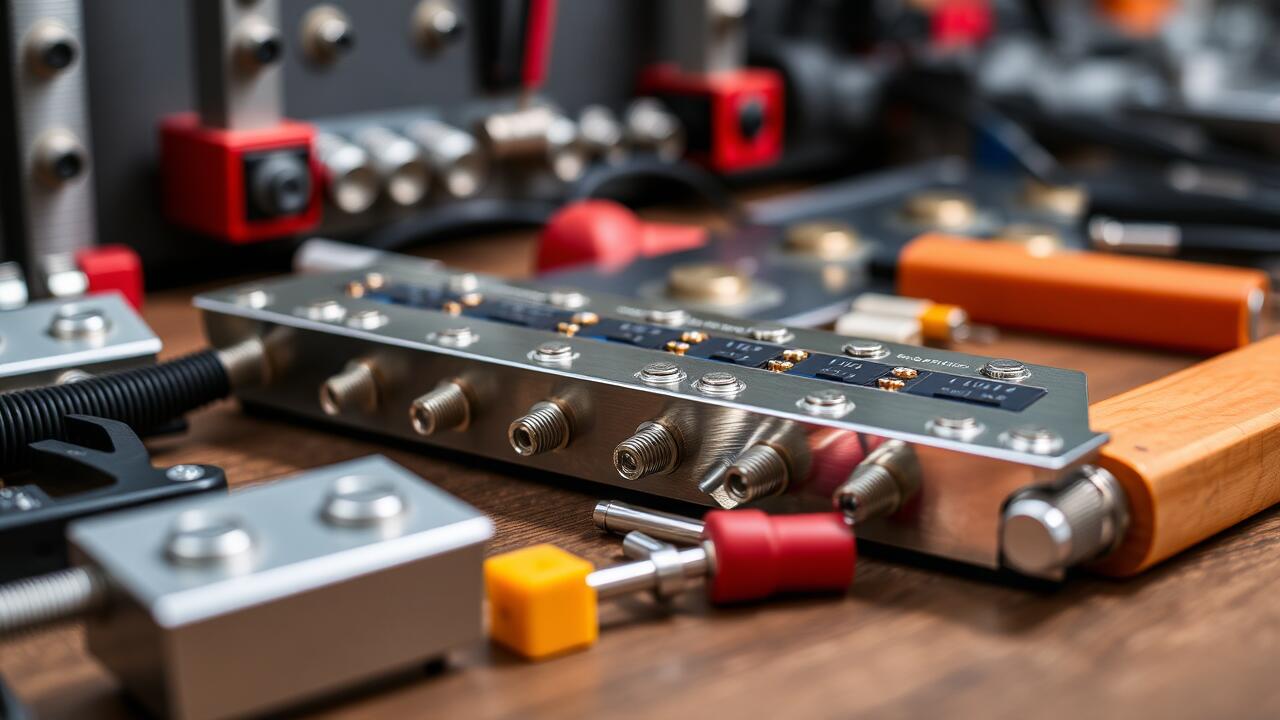
Standard vs. Custom Busbar Products
Standard busbar products offer a reliable solution for many electrical distribution needs. These products often cater to general applications across various sectors such as the transportation industry. Utilizing aluminum alloy foil, standard busbars are designed to accommodate feeder busways effectively. They are suitable for outdoor applications where durability is essential, making them a popular choice for projects that require a balance between efficiency and cost.
Custom aluminum busbars provide tailored solutions for specific requirements within transportation industries. These busbars can be designed to integrate seamlessly with components like auto body panels, ensuring compatibility and enhanced performance. Customization options enable the metalizing process to create panels that suit unique project demands, whether for high-load applications or specific dimensional constraints. This adaptability is crucial for maximizing operational efficiency in specialized environments.
Innovations in Busbar Technology
Recent advancements in busbar technology have led to the development of custom aluminum busbars that cater to specific electrical needs. These innovations focus on improving efficiency while minimizing space requirements in various applications, including low voltage busses. Enhanced bar design allows for better heat dissipation and integration within metal enclosures. The ability to customize aluminum busbars for unique configurations means they can be seamlessly integrated into trailer construction, rail systems, and specialized vehicles.
The introduction of modular busbar systems has revolutionized installation processes. These systems simplify the setup by allowing for quick assembly and disassembly without sacrificing performance. Carts designed to support the transport and installation of these custom aluminum busbars ensure an efficient workflow. The ongoing evolution within busbar technology not only enhances the functionality of the bars but also expands their application across diverse sectors, making them ideal for various industrial and commercial needs.
Installation and Maintenance of Aluminum Busbars
Proper installation and maintenance of custom aluminum busbars play a crucial role in ensuring optimal performance and longevity in various electrical systems. The use of pure aluminum conductivity allows these busbars to effectively handle high voltage applications while maintaining efficiency. It is essential to securely mount the busbars on racks within a warehouse facility to prevent any mechanical stress during operation. Regular inspections of manufacturing parts and the overall condition of heavy-duty applications are necessary to identify any signs of wear or damage. By adhering to a thorough maintenance routine, one can ensure that custom aluminum busbars continue to function reliably and contribute to the overall efficiency of the electrical infrastructure.
Maintenance Task | Frequency | Description |
---|---|---|
Visual Inspection | Monthly | Check for signs of corrosion, wear, or any physical damage to the busbars. |
Tightening Connections | Annually | Ensure all connections are secure to prevent electrical resistance and overheating. |
Cleaning | Quarterly | Remove dust and debris to maintain optimal conductivity and prevent overheating. |
Thermal Imaging | Biannually | Utilize thermal imaging to identify hot spots that may indicate electrical issues. |
Conclusion
Custom aluminum busbars offer a versatile solution for electrical systems, combining lightweight properties with high conductivity. These busbars can be tailored in various thicknesses to meet specific design requirements, ensuring optimal performance in diverse applications. A custom manufacturer can produce busbars in different shapes, including flat bars and cylindrical tubes, catering to unique installation needs. The manufacturing process emphasizes precision, ensuring that each product meets or exceeds industry standards for quality and durability. Stainless steel options provide additional flexibility for environments with corrosive elements, but custom aluminum busbars remain a popular choice due to their efficiency and cost-effectiveness.
FAQS
What factors should be considered when selecting an aluminum bus bar for high voltage applications?
When choosing the correct bus bar for high voltage applications, it’s crucial to understand aluminum busbar conductivity to ensure efficient electrical performance. The busbar production department must utilize high-quality aluminum coils and sophisticated equipment to fabricate bus bars that meet specific industry standards. Proper design and fabrication will enhance the overall effectiveness and longevity of the aluminum can used in conjunction with the busbar system.
How does the design of a high voltage bus affect its performance and reliability?
The design of a high voltage bus is crucial for its performance and reliability. Factors such as material choice, thermal management, and mechanical strength impact the effectiveness of a high voltage bus. Proper design ensures optimal conductivity, heat dissipation, and minimizes the risk of failure in demanding conditions.
What are the advantages of using custom aluminum busbars in electrical systems?
Custom aluminum busbars offer several advantages in electrical systems, including excellent conductivity, lightweight construction, and corrosion resistance. These benefits contribute to efficient power distribution and can be tailored to the specific needs of the application, enhancing both performance and reliability.
What are the potential applications for custom aluminum busbars in industrial settings?
Custom aluminum busbars can be utilized in a variety of industrial applications, including power distribution, renewable energy systems, and electric vehicle charging infrastructure. Their lightweight nature and excellent conductivity make them ideal for use in environments where space and efficiency are crucial.
How can custom aluminum busbars improve the efficiency of electrical systems?
Custom aluminum busbars can enhance the efficiency of electrical systems by providing tailored solutions that optimize current distribution and reduce energy losses, ensuring better performance and reliability in various applications.